What is Porosity in Welding: Usual Sources and Reliable Remedies
Wiki Article
Unraveling the Mystery of Porosity in Welding: Tips for Decreasing Flaws and Making The Most Of Quality
In the elaborate globe of welding, porosity remains a relentless challenge that can dramatically impact the top quality and honesty of bonded joints. Recognizing the variables that add to porosity development is important in the search of flawless welds. By unwinding the mystery of porosity and applying efficient methods for flaw minimization, welders can raise the criteria of their job to accomplish remarkable top quality end results. As we dig right into the depths of porosity in welding, uncovering the keys to its prevention and control will certainly be paramount for professionals seeking to grasp the art of premium weldments.Recognizing Porosity in Welding
Porosity in welding, an usual problem run into by welders, refers to the visibility of gas pockets or spaces in the bonded product, which can compromise the stability and top quality of the weld. These gas pockets are generally trapped during the welding procedure due to various variables such as improper securing gas, polluted base materials, or inaccurate welding criteria. The development of porosity can compromise the weld, making it susceptible to fracturing and deterioration, ultimately causing structural failings.Recognizing the source of porosity is essential for welders to successfully stop its incident. By acknowledging the relevance of preserving appropriate gas shielding, ensuring the tidiness of base products, and optimizing welding setups, welders can dramatically reduce the possibility of porosity formation. Furthermore, using methods like preheating the base product, employing appropriate welding strategies, and conducting detailed examinations post-welding can better assist in decreasing porosity issues. In general, a comprehensive understanding of porosity in welding is crucial for welders to generate top notch and long lasting welds.
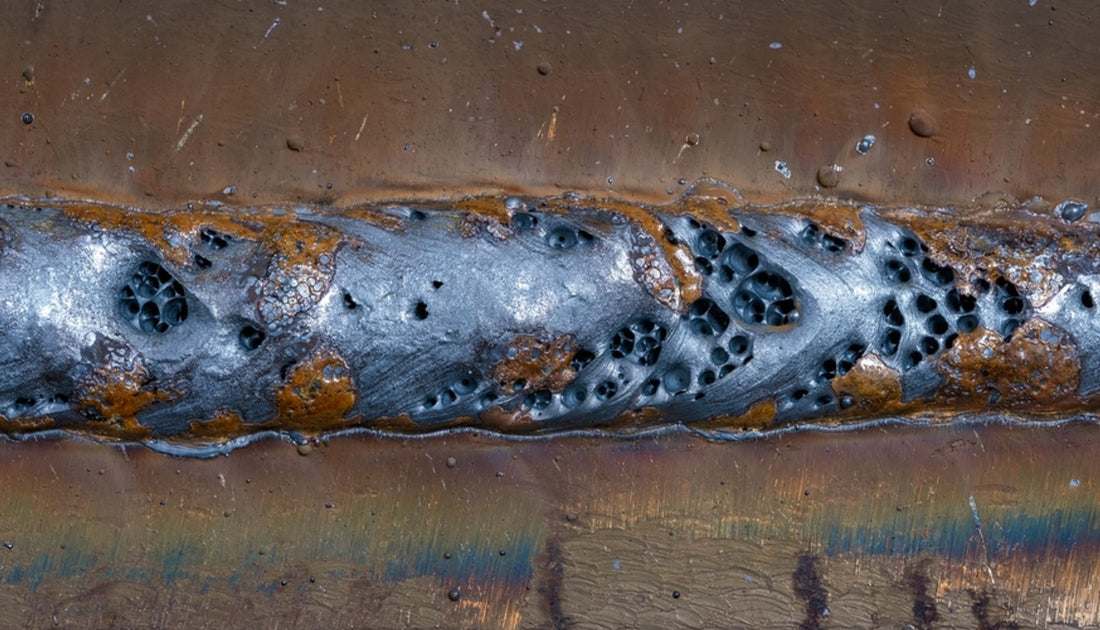
Typical Sources Of Porosity
When examining welding processes for potential quality problems, recognizing the typical reasons for porosity is necessary for maintaining weld honesty and stopping structural failures. Porosity, characterized by the presence of tooth cavities or spaces in the weld metal, can considerably jeopardize the mechanical residential properties of a welded joint. One usual cause of porosity is improper securing gas protection. Inadequate shielding gas flow rates or inappropriate gas mixtures can lead to atmospheric contamination, leading to porosity development.
One more widespread root cause of porosity is the existence of wetness and pollutants on the surface area of the base steel or filler material. When welding materials are not appropriately cleaned up or are exposed to high degrees of moisture, the vaporization of these pollutants throughout welding can develop gaps within the weld grain. Additionally, welding at inappropriate specifications, such as exceedingly high traveling rates or currents, can create excessive turbulence in the weld swimming pool, capturing gases and causing porosity. By addressing these usual reasons with proper gas securing, material prep work, and adherence to optimum welding criteria, welders can decrease porosity and enhance the quality of their welds.
Techniques for Porosity Avoidance
Executing efficient safety nets is important in reducing the event of porosity these details in welding procedures. One technique for porosity prevention is ensuring correct cleansing of the base steel before welding. Pollutants such as oil, grease, corrosion, and paint can result in porosity, so extensive cleaning using suitable solvents or mechanical techniques is essential.
Making use of premium filler products and protecting gases that are appropriate for the base steel and welding procedure can significantly lower the risk of porosity. Additionally, maintaining proper welding criteria, such as voltage, existing, take a trip rate, and gas circulation price, is vital for porosity prevention.
Furthermore, employing proper welding techniques, such as preserving a regular travel rate, electrode angle, and arc length, can aid stop porosity (What is Porosity). Ample training of welders to ensure they comply with finest practices and quality control procedures is additionally necessary in decreasing porosity problems in welding
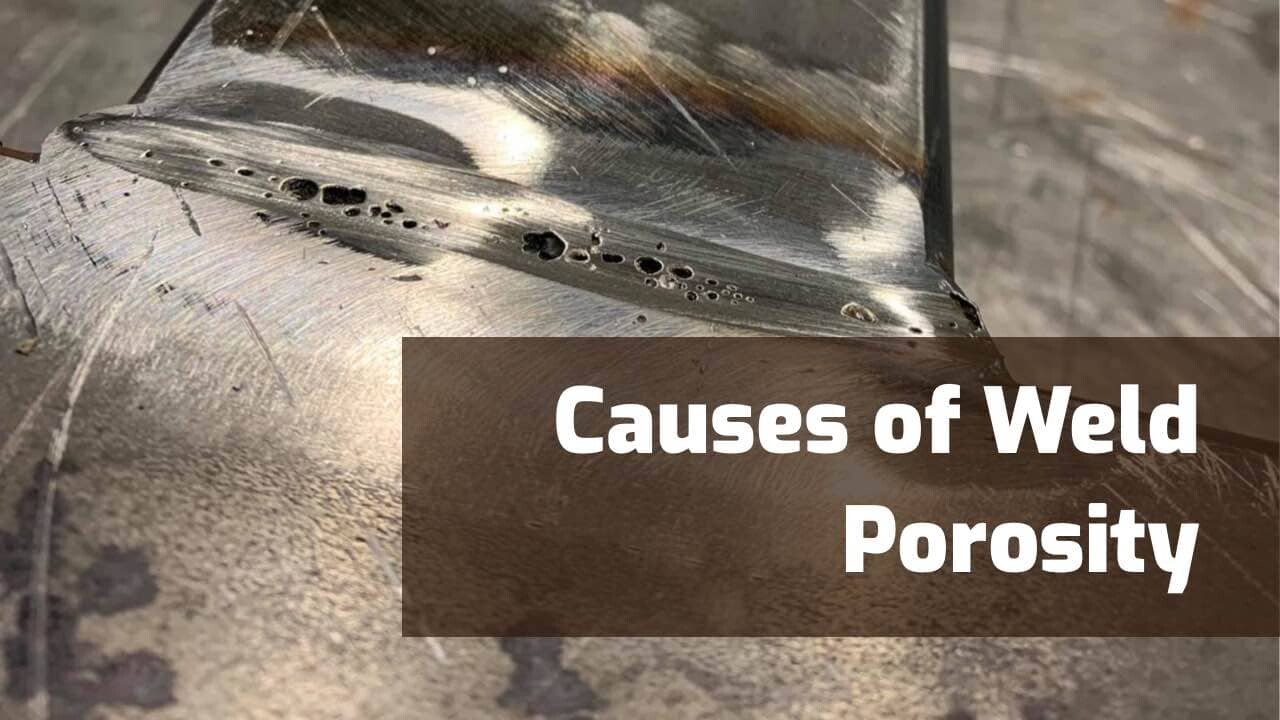
Best Practices for High Quality Welds
One trick technique is maintaining correct sanitation in the welding location. Completely cleaning the work surface and click for more info surrounding location before welding can aid mitigate these problems.An additional finest practice is to meticulously select the proper welding criteria for the certain products being signed up with. Appropriate parameter choice guarantees ideal weld penetration, fusion, and overall high quality. Making use of premium welding consumables, such as electrodes and filler steels, can dramatically influence the last weld high quality.
Importance of Porosity Control
Porosity control plays a critical role in ensuring the honesty and high quality of welding joints. Porosity, characterized by the presence of tooth cavities or spaces within the weld steel, can significantly endanger the mechanical residential properties and architectural honesty of the weld. Extreme porosity damages the weld, making it much more susceptible to splitting, deterioration, and total failure under operational tons.Effective porosity control is vital for maintaining the desired mechanical homes, such as toughness, ductility, and strength, of the bonded joint. What is Porosity. By minimizing porosity, welders can enhance the total quality and reliability of the weld, ensuring that it satisfies the efficiency needs of the intended application
In addition, porosity control is essential for accomplishing the desired visual look of the weld. Extreme porosity not just weakens the weld however also diminishes its visual appeal, which can be important in markets where visual appeals are necessary. Correct porosity control strategies, such as using the appropriate protecting gas, managing the welding criteria, and making sure correct tidiness of the he said base materials, are essential for creating high-grade welds with very little defects.

Verdict
Finally, porosity in welding is a common defect that can compromise the high quality of the weld. By understanding the root causes of porosity and implementing proper prevention techniques, welders can decrease issues and attain greater quality welds. It is vital to manage porosity in welding to make sure the stability and stamina of the final product. Executing finest practices for porosity control is vital for achieving ideal welding results.Report this wiki page